EffektiV: Virtual Stresstests for Robots
Overview
Manufacturing plants of the future, the so-called cyber-physical Production Systems (CPPS), are highly complex, intelligent systems, which consist of a large number of heterogeneous components: software, microelectronics, power electronics, sensors, actuators. In this context, motion control systems, which form the core of those systems, coordinate the control of specific parts like conveyor belts and robotic arms for fast and highly accurate positioning. To ensure the functional safety, such as given by the ISO 26262 standard, for instance, a variety of methods can be applied: Fault Tree Analysis (FTA), Failure Mode and Effects Analysis (FMEA), Electromagnetic Compatibility Analysis (EMC), but also basic tests by simulation to verify the functional correctness. However, the final test of those systems is mostly still based on physical prototypes. Therefore, certain faults can hardly or not provoked and can thus hardly or not verified due to some physical conditions and side effects. For this reason, so-called virtual prototypes are applied in which physical hardware is replaced by hardware models that may become available already at earlier stages in the design process.
The EffektiV project explores new technologies and tool chains for functional safety verification of motion control systems based on virtual prototypes.
EffektiV is a project funded by the German Federal Ministry for Education and Research (grant no: 01IS13022), which is carried out in cooperation with Bosch, 360直播吧mens, and Infineon Technologies as industrial partners.
The tool developments in the project are based on the IEEE 1666-2011 system description language SystemC for the discrete and on SystemC-AMS for the analog system components, where for software components the software emulator QEMU is applied in conjunction with the integration of commercial tools such as MATLAB/Simulink. Our work in the project focuses on the development of fault models for analog subsystems, the integration and implementation of specific instruction set architectures as well as on the implementation of a project demonstrator.
The development of analog fault models is generally not very advanced in the context of a fault effect simulation. Based on the safety standards IEC 60730 and ISO 26262 we are working on a SystemC-AMS library for fault effect simulation of analog components. This includes, for example, the parameterized stimulation of frequency and amplitude variations as well as voltage surges and drops at connecting wires and power supply lines.
In conjunction with SystemC we apply QEMU as an open source virtual platform for target-specific software execution. We currently work on the implementation of the complete TriCore ? instruction set with over 700 instructions. A first version was already published with QEMU 2.2 (wiki.qemu.org) by the end of 2014. The TriCore ? instruction set was defined by the Infineon Technologies and is applied in the microcontroller cores of the AURIX ? and AUDO? processor families.
In cooperation with Infineon Technologies, we finally work on the implementation of a project demonstrator for fault injection, which based on the robolink?-multi-axis system of the igus GmbH.
Key Facts
- Grant Number:
- 01IS13022
- Project type:
- Sonstiger Zweck
- Project duration:
- 06/2014 - 05/2017
- Funded by:
- Bundesministerium für Bildung und Forschung (BMBF)
More Information
Contact
If you have any questions about this project, contact us!
apl. Prof. Dr. Wolfgang Müller
System and Circuit Technology / Heinz Nixdorf Institut
Apl. Professor
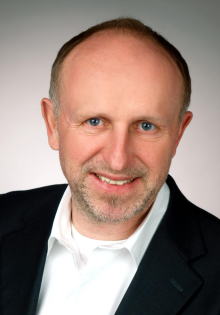